What are the Design Guidelines of Rotational Molding?
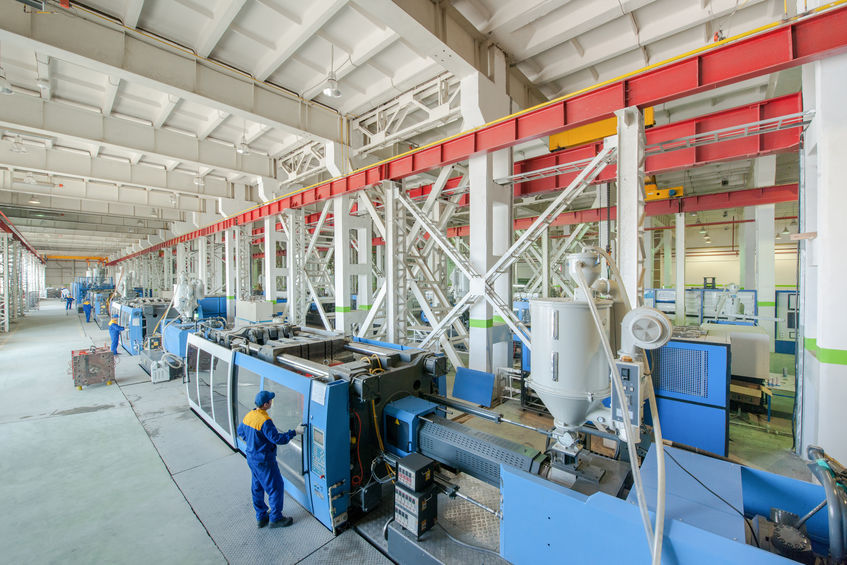
The design guidelines of rotational molding mark the beginning of a successful rotational molding project. The perfect design for a rotomolded component is that any hollow shape where the design elements are meshed in smoothly. This smooth blend causes product strength, which is a must for manufacturing products like boats, tanks, pallets, bins, housings and assemblies. It also guarantees efficient production at http://fibertechinc.net/.
Here’s what is needed
The design guidelines of rotational molding designs have three most basic requirements. The rotomolded part must always:
- Fulfill the end use or functional needs
- Be responsible for limitations related to materials or processing
- Support budget friendly production techniques
When it comes to selecting plastic, know to determine the various rotational molding materials that have varied properties and processing needs. For instance, polycarbonate has low mold shrinkage and hard flow and crystalized polyethylene has high mold shrinkage and easy flow. Usually, the plastic materials with the lowest shrinkage factor give away the most dimensionally stable components. The design engineers also need to determine that the rotational molding is a low pressure process. It means that the two halves of the rotational mold don’t need high pressure clamping. When you compare it to the injection molding, then the rotomolded components may need larger tolerance rates on component dimensions that are perpendicular to the parting line of the mold. The mold design and construction impact the component quality as well.
Component details
The details of the component design also aid the success of the rotomolding project. The details encompass the following:
- Nominal wall thickness
- Wall thickness uniformity
- Varying wall thickness
- Flatness considerations
- Minimum wall separation
- Corner angle limits
- Reinforcing ribs
- Kiss off ribbing
- Draft angles
- Corner Radiuses
- Undercuts
- Tolerances
Materials needed for rotomolding
- LLDPE rotomolding
This makes the use of the linear low density polyethylene or LLDPE which is a durable plastic that bears good impact and puncture tolerance when high tensile strength. The applications for LLDPE rotational molding are buckets, ranks, toys, bins, containers, and recreational things. The pros of this rotomolding are flexible designs, color matching and custom colors.
- HDPE rotomolding
This utilizes the high density polyethylene which is a strong and lightweight thermoplastic. This rotomolding process can support complicated designs and huge products like the ones used by food in the food processing industry.