The Importance of Quality Control in Industry Manufacturing
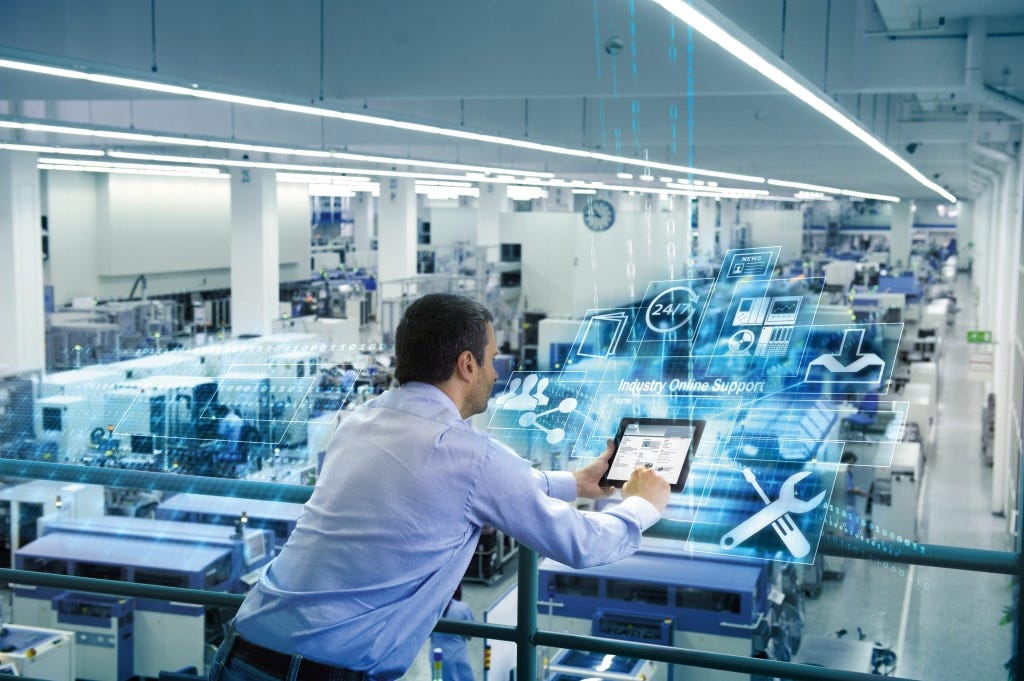
In the fast-paced world of manufacturing, where high standards and customer satisfaction are paramount, the importance of quality control cannot be overstated. Quality control (QC) ensures that products meet specific standards of quality and perform as expected, minimizing defects and ensuring reliability. This process is essential for maintaining a company’s reputation, reducing costs, and meeting regulatory requirements. The following sections explore the key reasons why quality control is critical in the manufacturing industry and how it contributes to long-term success.
1. Ensuring Product Consistency
One of the primary purposes of quality control in manufacturing is to ensure product consistency. Consistency is key to building trust with customers and maintaining brand loyalty. When a manufacturer produces a product, it must meet a certain set of criteria, such as size, weight, material quality, and durability. Without quality control measures in place, there is a significant risk of variance from one unit to the next. Even slight inconsistencies can impact the performance of the product and affect its usability.
Through quality control, manufacturers can establish standard operating procedures (SOPs) and implement rigorous testing protocols. These measures allow manufacturers to detect and correct any variations during the production process, ensuring that every unit produced adheres to the same high standards. As a result, customers receive the same product experience with each purchase, reinforcing their confidence in the brand.
2. Reducing Defects and Waste
Manufacturing processes inevitably generate some level of waste and defects. However, without a comprehensive quality control system, these issues can escalate, leading to higher production costs and increased waste. For instance, defective products that are not identified early in the production process often lead to material wastage, increased rework, and more significant operational delays.
By integrating quality control into every phase of production, manufacturers can quickly identify defects before they escalate into larger problems. Techniques such as statistical process control (SPC) and regular inspections allow for the detection of deviations in production parameters. By addressing these issues early, manufacturers can reduce scrap rates, minimize rework, and prevent defective products from reaching the market. This not only lowers costs but also conserves resources, making manufacturing operations more efficient and sustainable.
3. Enhancing Customer Satisfaction
Customer satisfaction is at the heart of any successful business, and quality control plays a vital role in achieving this goal. In an era where consumers have access to vast amounts of information and alternatives, product quality is often the deciding factor in purchasing decisions. A single defect or subpar product can damage a brand’s reputation, resulting in lost sales, negative reviews, and reduced customer loyalty.
Quality control ensures that products meet the expectations set by the manufacturer and the promises made to customers. Whether it is a durable and high-performance product or one that meets safety standards, quality control ensures that products are reliable and functional. Consistent product quality leads to customer satisfaction, which ultimately strengthens the brand and fosters repeat business. By investing in quality control, manufacturers demonstrate a commitment to meeting customer needs, which helps cultivate long-term relationships and trust.
4. Complying with Industry Standards and Regulations
Manufacturing industries across the globe are governed by a variety of regulations and standards, which are designed to ensure that products are safe, reliable, and meet specific performance benchmarks. For instance, industries such as automotive, pharmaceuticals, and food production are subject to stringent regulatory guidelines that are enforced by government agencies. Failure to comply with these regulations can result in fines, product recalls, and even the shutdown of operations.
Quality control is essential for ensuring compliance with these regulations. By systematically testing and inspecting products, manufacturers can ensure they meet industry-specific standards and pass regulatory audits. In sectors where safety is critical, such as aerospace or medical device manufacturing, quality control processes are vital in ensuring that products meet safety requirements and do not pose a risk to users. A solid quality control system not only reduces the risk of regulatory non-compliance but also minimizes the chances of recalls or lawsuits, which can damage a company’s reputation and bottom line.
5. Minimizing Production Costs
Although quality control requires an investment in both time and resources, it can significantly reduce production costs in the long run. A robust quality control process can prevent the need for costly repairs, rework, or product recalls. The expense of addressing defects after the product has been shipped to the customer is much higher than preventing them during production.
Quality control also helps in optimizing resource utilization. By identifying production inefficiencies and areas of waste, manufacturers can adjust their processes to maximize the use of materials, reduce energy consumption, and streamline operations. Additionally, regular audits and testing help identify process improvements that can lead to cost savings. Through quality control, manufacturers can identify ways to optimize labor costs, minimize downtime, and prevent costly delays.
6. Supporting Continuous Improvement
Quality control plays a crucial role in fostering a culture of continuous improvement within a manufacturing organization. As manufacturers identify defects, inefficiencies, or areas for optimization, they can use this data to improve processes over time. Quality control isn’t a one-time event but an ongoing process that encourages companies to constantly assess their operations, gather feedback, and make adjustments.
The feedback generated from quality control activities, such as root cause analysis and defect tracking, can be used to implement corrective and preventive actions (CAPA). By addressing these issues, manufacturers can improve their production processes, enhance product quality, and stay competitive in the market. This continuous improvement process not only benefits the company but also ensures that customers consistently receive better products.
7. Protecting Brand Reputation
A manufacturer’s reputation is one of its most valuable assets. In today’s interconnected world, a company’s reputation can be built or destroyed quickly based on the quality of its products. Customers expect manufacturers to deliver products that meet high standards, and they are quick to share their experiences—good or bad—through online reviews, social media, and word of mouth.
Quality control protects the brand reputation by ensuring that only products that meet rigorous quality standards reach the market. By reducing defects and minimizing the risk of recalls, quality control helps companies maintain their brand’s positive image. Moreover, when customers perceive a brand as trustworthy and consistent, they are more likely to return for future purchases and recommend the products to others. A commitment to quality, supported by a strong quality control process, can establish a reputation for excellence and build customer loyalty.
8. Promoting Employee Engagement and Accountability
Quality control also plays a vital role in promoting employee engagement and accountability. When employees are actively involved in the quality control process, they gain a better understanding of how their actions impact product quality. This sense of responsibility can lead to increased job satisfaction and a stronger commitment to excellence.
Employees who are trained in quality control techniques are empowered to identify and resolve issues during production, ensuring that quality is maintained throughout the process. Encouraging a culture of quality within the workforce promotes teamwork, improves morale, and enhances productivity. Employees feel a sense of pride in knowing that their work contributes to the creation of high-quality products.
Conclusion
Quality control is an indispensable part of the manufacturing process, impacting nearly every aspect of production. By ensuring product consistency, reducing defects, enhancing customer satisfaction, and complying with industry standards, quality control is vital to a manufacturer’s success. Additionally, it helps minimize production costs, supports continuous improvement, protects brand reputation, and fosters a culture of employee engagement. Manufacturers who prioritize quality control are better positioned to thrive in an increasingly competitive market and meet the ever-growing expectations of customers. Investing in robust quality control systems is not just a requirement; it is a strategic decision that yields significant long-term benefits.