Maximizing Equipment Efficiency and Minimizing Costs: Industrial Machinery Maintenance Best Practices
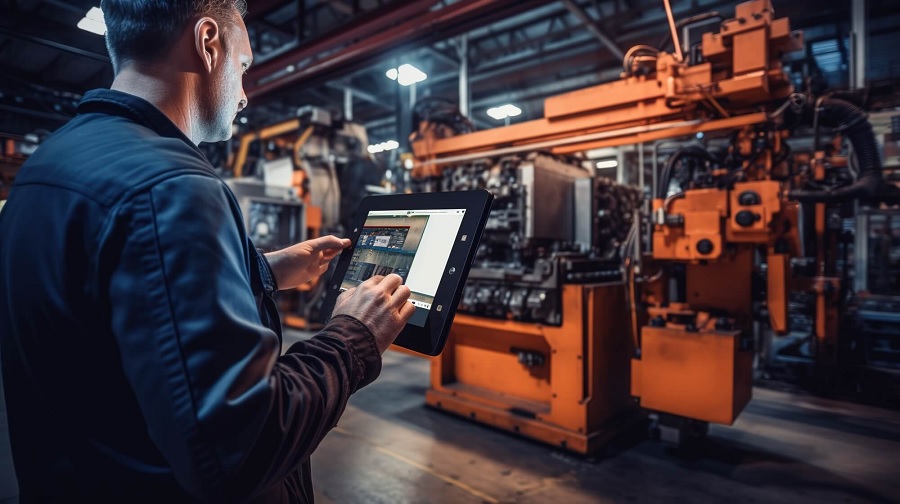
The effective maintenance of industrial machinery is essential for maintaining productivity and controlling costs. As the global market for MRO continues to expand, industries are adopting more advanced maintenance strategies to improve performance and reduce downtime. In this article, we explore key strategies to streamline maintenance and boost equipment efficiency.
Unplanned downtime is a common challenge for many industries, with aging equipment, mechanical failures, and operator errors contributing to disruptions. A proactive solution is to use low-maintenance components such as ultrasonic clamp-on meters. These components require minimal servicing and are less prone to failure, reducing downtime and maintenance needs.
Preventive maintenance (PM) remains a standard practice, with 76% of manufacturers scheduling regular inspections to avoid equipment breakdowns. While PM is effective, it contributes to the total cost of ownership, which can add up over time and impact profitability.
Predictive maintenance (PdM) offers a more advanced solution by using real-time data to monitor the condition of machinery and predict when repairs are necessary. PdM helps businesses avoid unnecessary maintenance and reduce downtime by addressing problems before they escalate. With 41% of manufacturers already using PdM, it is a growing trend that has been shown to save up to 12% in maintenance costs.
By adopting these strategies, businesses can lower maintenance costs, improve machinery performance, and increase overall operational efficiency. For more information on the impact of predictive maintenance, check out the infographic by Emerson.